The LiBER solution has the unique characteristic of sharing the basic project, the components, and the production process among different final products even very different from each other. This approach makes the LiBER solution competitive for production volumes between 10 and 100MW/year, thanks to a production process that combines manual and automatic assembly in the best possible way. Higher volumes can be managed with high-capacity automatic lines.
brick design & brick manufacturing process
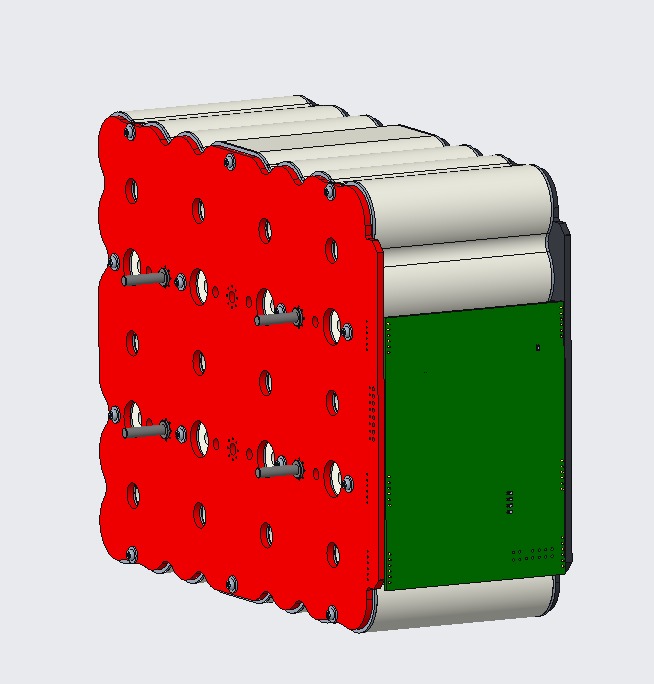
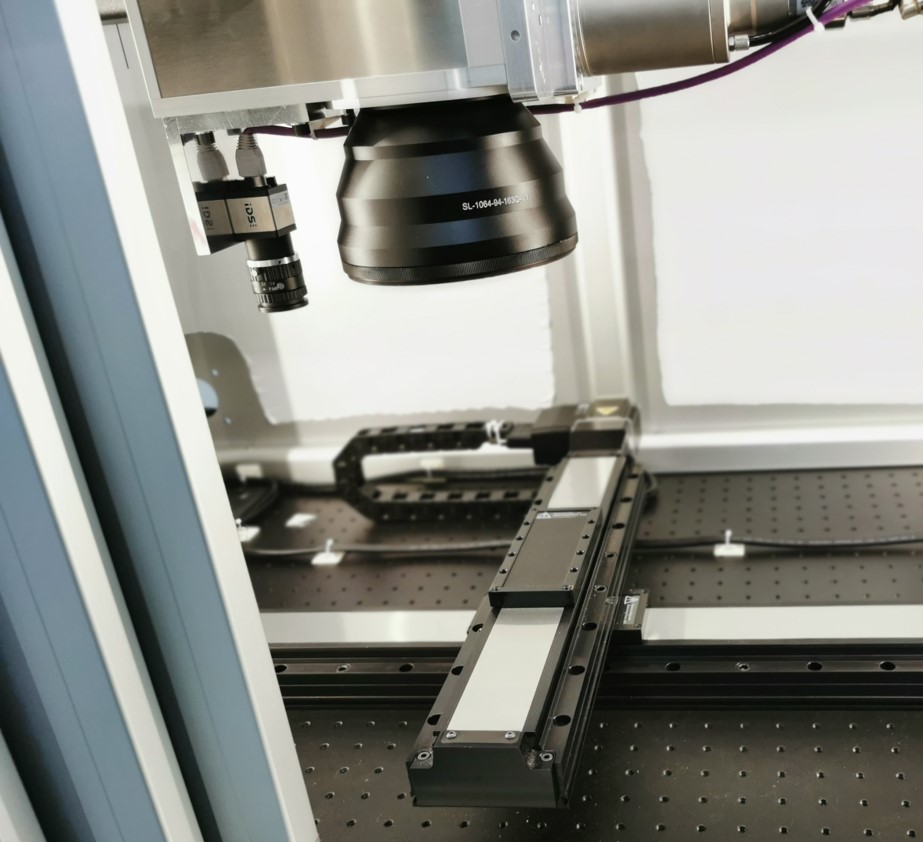
Use of the same process for multiple products
Use of the same product for many final applications
Robotized assembly
Integration simplicity
Safe working environment
Medium to large production volumes
Quality of the integration
Module design and module assembly process
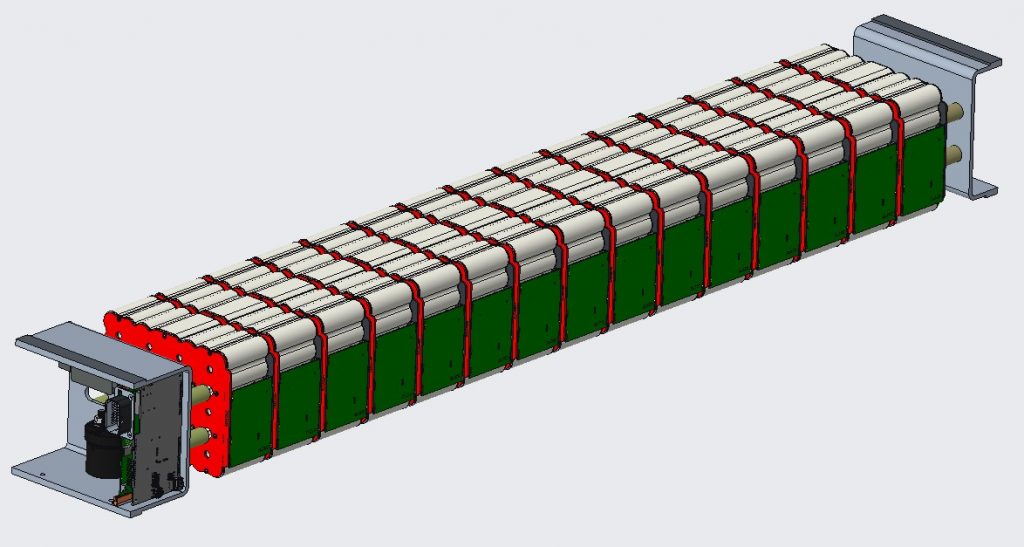

Use of the same process for multiple products
Specialization of the product for the final applications
Manual assisted assembly
Quality
Safe working environment
Small to medium production volumes
Pilot line
LIBER has a prototyping workshop and a pilot production line having a production capacity up to 10MWh/year, located in Bologna-ITALY.
qualified process
combination of robotized and manual operations for the assembling the brick
manual operations for assembling the modules
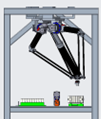
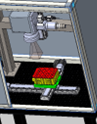
Cylindrical cells qualification stations
Prismatic cells qualification and equalization station
automatic cylindrical cell tracking and handling
laser welding station
Brick qualification station
Manual module assembly station
Module qualification station
Robotized line
LIBER has designed a robotized line for the assembling of brick based on the same core processes of the pilot line, which is able to reach a production volume of 80MWh/year.
qualified process
automatic assembling of the brick
Cylindrical cells qualification stations
Automatic cylindrical cell tracking and handling
Automated laser welding station
Automated brick qualification station
Robotized handling of parts and brick
Automatic brick formation